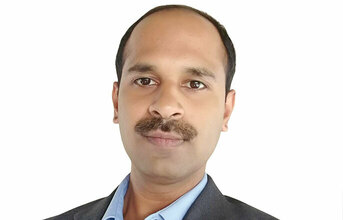
What is digital manufacturing and what use cases deliver maximum benefits?
Digital manufacturing, also known as Industry 4.0 or smart manufacturing, refers to the use of digital technologies and data-driven processes to optimise and streamline various aspects of manufacturing operations. It represents a transformative shift from traditional manufacturing methods to more automated, connected, and datacentric approaches, while also tapping into new technologies like AI, VR, and AR.
The current landscape is being transformed by rapid advancements and increasing complexity in manufacturing technologies. Digital manufacturing has enhanced business outcomes, with improvements of up to 88 per cent in productivity, 74 per cent in profitability, and 48 per cent in quality. The use cases of digital manufacturing that can deliver maximum benefits vary depending on the industry, which includes predictive maintenance, robotics, automation, and smart factory optimisation using tools such as digital twins to optimise production.
What sort of investments are needed to integrate IoT in digital manufacturing?
Digital manufacturing is the next step in industrial IT and software. With IoT, digital manufacturing can yield significant benefits, but it also requires careful planning for the investments to be successful.
Just like every industry, the specific investments required will depend on the scope and scale of the digital manufacturing initiative. Largely, OEMs would require an updated inclusive strategy to introduce connectivity to legacy machines, robust cloud and connectivity infrastructure, robotics, secure data storage management, analytics tools with AI/ML, and device management and maintenance. Upskilling of employees, maintenance of equipment, scalability, and future expansions are also factors that would require an investment, especially in the long run.
Additionally, investing in advanced sensors, edge computing technology, and regulatory compliance will go a long way. Another area which is overlooked is the right partnership with system integrators for run management, which is critical for a flawless Industry 4.0 implementation.
What is the impact of digital twins for design for manufacturing (DFM) and how is it transforming manufacturing operations?
A digital twin is a virtual representation of a physical object or system, and in the context of manufacturing, it refers to a virtual model that mirrors a physical product, process, or facility. Digital twins have a lot of potential, and its use has a profound impact on Design for Manufacturing (DFM) and can transform manufacturing operations.
The way we run digital twins is going to be run on simulation, which is easier said than done. Digital twins have a significant impact on the DFM process in various ways. For instance, designers can use it to optimise the geometry of a product and even customise it, ensuring that it can be produced efficiently and cost-effectively. It can also help in virtual prototyping, reducing the need for physical prototypes, continuous improvement, better design collaboration and thus reducing the overall cost. It also enhances efficiency and improves the overall product quality.
What are the roadblocks while implementing digital manufacturing and how to overcome them?
Every implementation is a transformative process, which comes with its set of challenges and rewards. As far as digital manufacturing is concerned, one of the most prominent challenges is the high investment initially. Companies can consider phased investment and run a cost-benefit analysis to secure investment. With the rise in security challenges, implementing digital manufacturing raises safety and privacy concerns. Interoperability and scalability are also among the challenges that one faces with digital manufacturing. Like any other implementation, transformation to digital manufacturing will also have issues with management change which can be mitigated with a well laid roadmap and right stakeholder involvement at every stage.
How predictive frameworks can facilitate sustainable manufacturing?
Sustainability is the keyword right now and predictive frameworks can play a crucial role in facilitating sustainable manufacturing by enabling more informed decision-making. There will be great visibility of performance metrics, production and operational KPIs and the live status of the overall manufacturing facility with such frameworks. In the long run, predictive frameworks can ensure sustainability by helping reduce waste, optimising resource usage, and minimising the impact on the environment. For instance, it can help with predictive maintenance by analysing equipment failures to schedule maintenance activities for a more energy-efficient downtime.
Continue Reading on Page 2